Author: Pradeep Devadass
Co-Authors: Guillem Perutxet Olesti, Jingyuan Meng, George Dwyer, Sam Turner-Baldwin, Ben Spong, Martyn Carter, Viktoria Viktorija
Abstract
Over the past three years, the B-made (Bartlett Manufacturing and Design Exchange) robotics lab has developed a course to teach applied robotics in the context of architecture, using blended and interactive teaching methods to make it inclusive. This presentation will focus on the lab’s collaboration with Autodesk, a leading software company, to ensure that the course and its content remain relevant to industry standards. The presentation will describe how student assistants, technicians, and academics have collaborated with the company to transfer knowledge to the course’s users. It will also discuss the efficacy of the course, which was demonstrated through staff and student workshops held in the Autumn Term of 2022, and its impact on practice, research, and academia.
Introduction
B-made provides a manufacturing-based education in a design-fuelled context to the students of BSA (Bartlett School of Architecture). B-made is a popular resource for staff, researchers, and students providing practical, contextual, and manufacturing-based education that enables the use of specialist equipment and processes. B-made has been hosting various robots of different specifications to address problems in architectural manufacturing and construction for almost a decade. To transfer this knowledge, B-made developed and evolved the ‘Robots’ Course which teaches robotic manufacturing in the context of architecture over the last 3 years.
Challenge
B-made robotics has presented several challenges and initiatives at the UCL conference 2021 and UCL conference 2022. Among these, a key challenge is imparting robotic programming skills to users from diverse backgrounds. Traditionally, programming robots for creative applications have been taught using visual coding tools such as Rhinoceros3D and Grasshopper3D. Two major drawbacks arise from the use of visual scripting. Firstly, it is time-consuming to learn, and generating toolpaths requires creating programming code from scratch. Secondly, if there are any errors or bugs in the script, detecting and identifying them can be difficult for another person, specifically the technician who needs to check the code before the robot executes the program. These errors can cause robotic collisions that may result in damage to the equipment or compromise user safety.
Reaching out to the industry
Although industrial software packages such as Powermill and Robotmaster offer robust programming methods for robots, they also come with a steep learning curve. As a result, B-made sought the expertise of Autodesk, a leading software company that specializes in developing CAD (Computer-Aided Design) and CAM (Computer-Aided Manufacturing) software for various industries, such as architecture, aerospace, and product design construction, to name a few. Autodesk has been working on integrating robotics plugins within its Fusion 360 software, a versatile CAD-CAM software that allows users to develop the design and develop manufacturing machine code within the same interface. At B-made, Fusion 360 is widely used for 3D printing, CNC, and other numerical manufacturing tools due to its user-friendly interface. Existing users of Fusion 360 could easily adapt to programming robots because of their familiarity with the software which was one of the key reasons why B-made quickly began exploring and testing the software. Autodesk provided exclusive early access to this software package through their fusion 360 insider, allowing B-made to program robots.
Knowledge Exchange
As this was a software package in development, three initiatives were taken to set up and establish a teaching pathway. 1) Setup and development of manufacturing processes with student assistants 2) Testing the workflow through a staff workshop 3) Testing the teaching pathway through a student workshop.
1. Setup and development of manufacturing processes
In August 2022, two student assistants were employed using funding from Bartlett’s Internal Research Fund (IRF) to aid in the creation of a digital twin of B-made’s robotic setup. The purpose was to test the workflow, which included simulating the digital robot, generating the robot code, and executing it in a digital environment. The team developed two manufacturing processes: Robotic 3D Printing of Clay and Robotic Milling of Timber. Integrating the digital process required extensive data exchange between B-made and Autodesk, with B-made providing robot and tool specifications and configuration setups, while Autodesk shared knowledge on incorporating the data into the software and how to use it. Due to the remote location of the Autodesk team, virtual conference meetings were used to facilitate knowledge exchange.
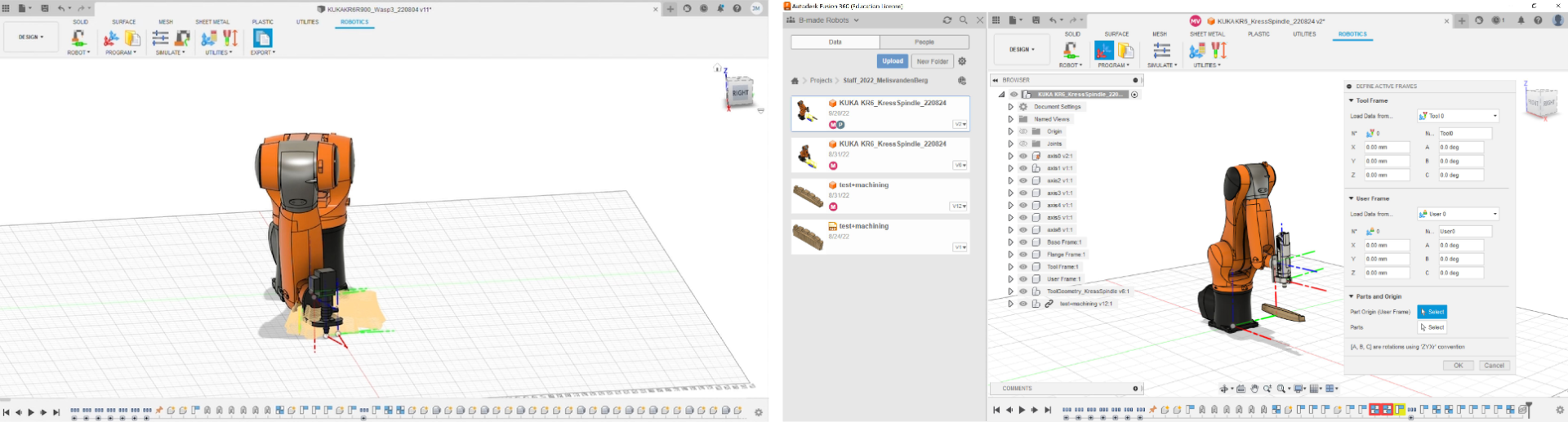
2. Testing the workflow through a staff workshop
In September 2022, following the development and implementation of the workflow, B-made conducted a staff workshop led by Jingyuan Meng and Guillem Perutxet Olesti to explore the two established manufacturing setups. Over ten participants who had no prior experience with robotics participated in the workshop. The workshop aimed to test and understand the nuances of using the software package, and participants provided feedback to Autodesk on errors encountered and the software’s intuitiveness. While the software is currently in development and cannot be used for programming complex robotic manufacturing projects such as assembly processes or advanced non-planar 3D printing, the majority of robotics users at B-made do not require such complexity and could adapt this workflow to realize their projects.
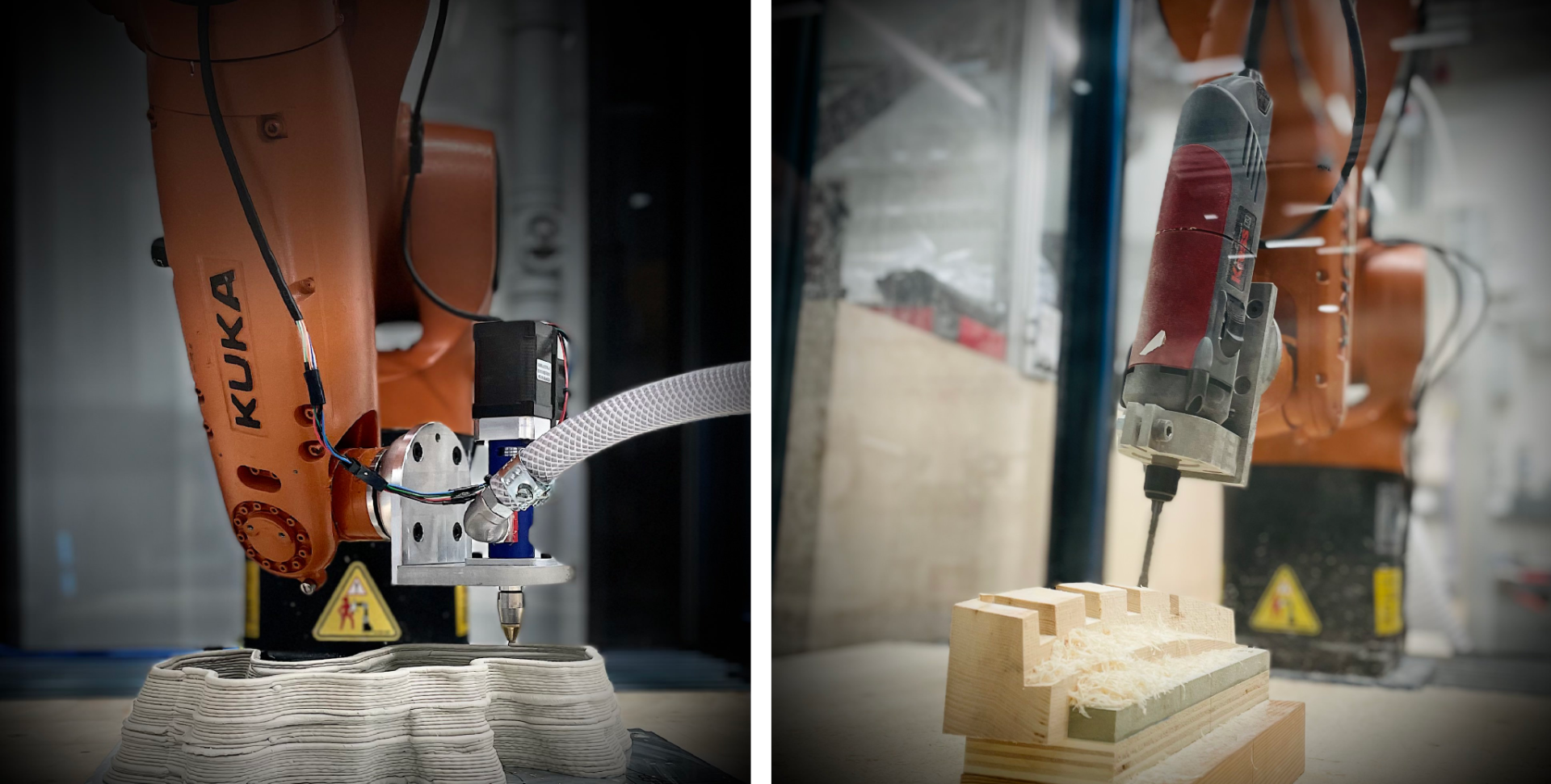
3. Testing the teaching pathway through a student workshop
As part of the first-year skilling module for Bio-Integrated Design students led by Guillem Perutxet Olesti, a week-long workshop was held in November 2022, focusing on the robotic 3D printing of clay. During the workshop, students utilized software platforms such as Rhinoceros 3D and Houdini to create their own geometries. They also learned how to navigate the manufacturing constraints and refine their designs accordingly. A total of 25 geometries were successfully manufactured, with students quickly mastering the programming code required for the robot. After the workshop, the crucial knowledge that needed to be conveyed was identified, and an asynchronous teaching pathway was created to supplement the existing robot course content.
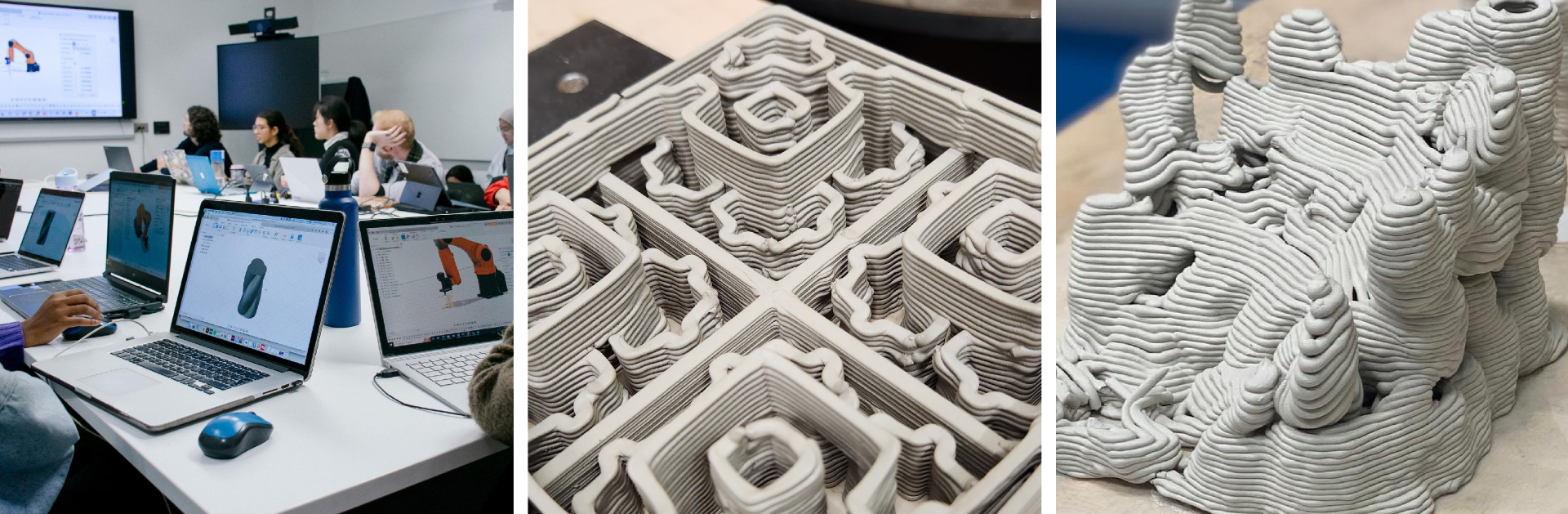
Impact on research, practice & academia
Oliver Wilton and Dan Pope are undertaking ongoing research supported by Jingyuan Meng, in collaboration with Weinerberger, that employed the pathway to facilitate the robotic additive manufacturing of a brick construction system intended for retrofitting the UK’s historic brick homes. The project delved into the creation of complex infills with varying densities for the brick, which would have been a challenging and laborious task to explore if not for the pre-set toolpaths available in Fusion360.
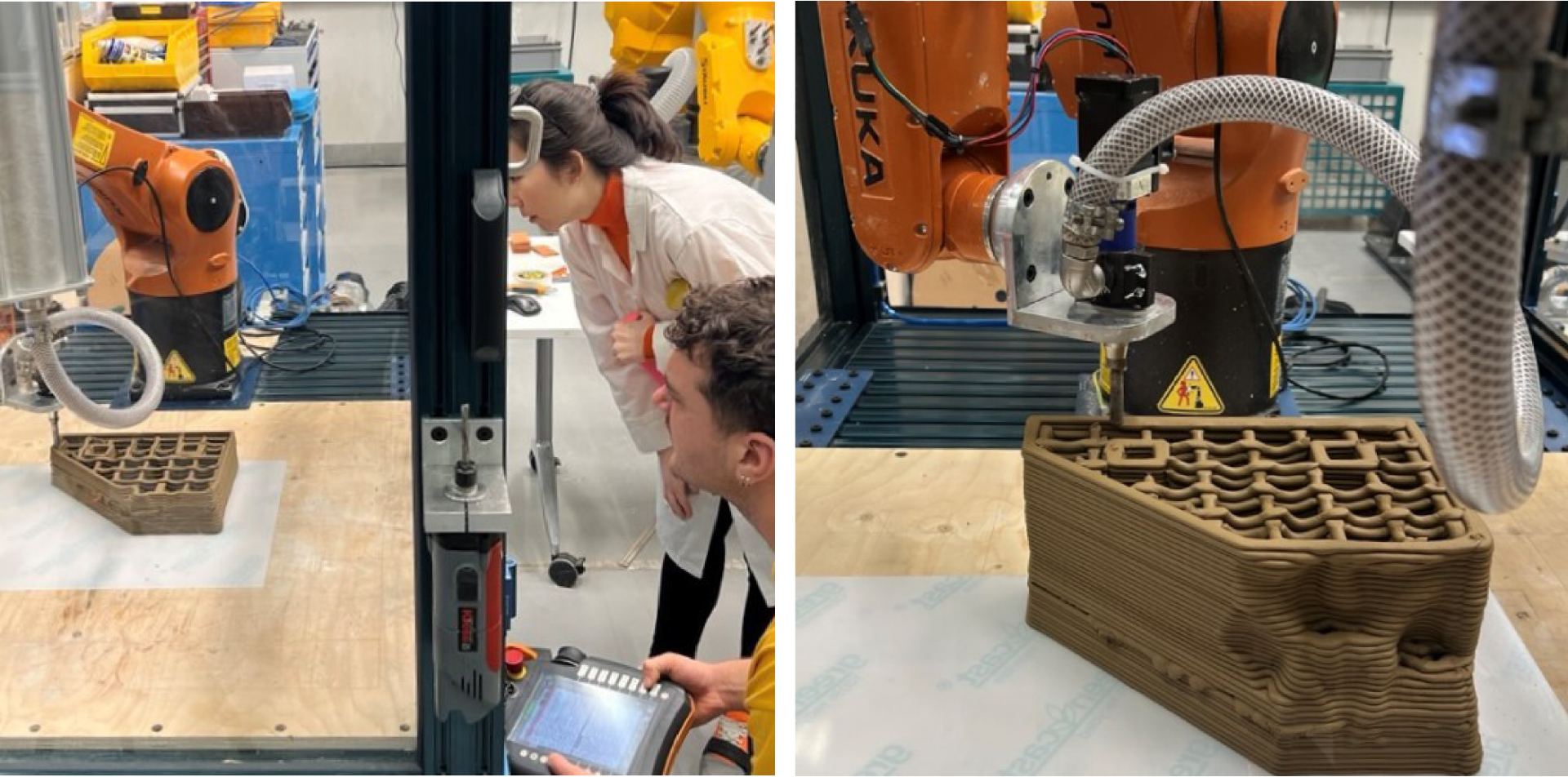
The software package was first tested on ABB and KUKA robots. Now the support has been extended to Staubli robots. The workflow will be tested on a research project led by Melis Van Den Berg and Sam Turner Baldwin in collaboration with independent artist Elpida Hadzi-Vasileva which will investigate 5DOF machining of bespoke timber joinery. The outcome of the project will be a public architectural installation.
Since January 2023, the Fusion 360 Robotics workflow and pathway have been put into practice as the primary programming method for Robotic 3D printing and milling. This implementation has resulted in the development of a reliable programming method, which has reduced the learning time required due to the interface being user-friendly, intuitive, and familiar to users.
By taking the initiative to approach the industry and conducting workshops, B-made robotics has successfully dispelled the myth of robots being complex and challenging equipment to use. As a result, there has been a surge in interest from students, researchers, staff, and practices in accessing robots, which has enabled various projects, contributing to the democratization of robotics at Bartlett.
Credits:
Autodesk Support: Alexandre Pinto
Student Assistants: Paul Kohlhaussen, Tom Ushakov
Staff Workshop Participants: Hamish Veitch, Robin Mather, William Victor Camilleri, Tom Davies, James Williamson, Melis van den berg, Sienna Griffin-Shaw, Cephas Bhaskar, Ben Lee
Student Workshop Participants: Maria Jose Creuheras Gonzalez, Rashneet Kaur Chhabra, Choi Wing Tse, Nathanael Gregory Myers, Edward Sameer Khoury, Gayatri Jain, Andrita Yuniza Orbandi, Yumeng Wei, Xinrui Cai, Sahda Salsabila, Farida Hany Radwan, Keren Lisa Permutti, Fang-Yu Liu, Daisy Rani Xavier, Natalie Rizk, Rida Iram Mughal, Sophia Layla Saleki, Isik Ogutcu, Kira Elise Mathias-Prabhu, Sophie Anne Kirkpatrick
B-made Managers: Mark Burrows, Niamh Grace
B-made Director: Peter Scully